Maximizing Your Welding WPS: Strategies for Improved Efficiency and Effectiveness
Maximizing Your Welding WPS: Strategies for Improved Efficiency and Effectiveness
Blog Article
Getting Welding Quality: Unveiling the Keys of WPS Implementation and Optimization
In the world of welding, attaining quality is a search that hinges on the careful implementation and optimization of Welding Procedure Specs (WPS) By delving right into the vital elements, strategies, obstacles, and best methods associated with WPS, a globe of welding excellence awaits those who are eager to explore its depths.
Relevance of WPS in Welding
The Value of Welding Procedure Specifications (WPS) in the welding market can not be overemphasized, functioning as the backbone for guaranteeing uniformity, top quality, and safety in welding operations. A WPS supplies comprehensive guidelines on just how welding is to be executed, consisting of essential variables such as materials, welding procedures, joint layout, filler metals, interpass and preheat temperature levels, welding currents, voltages, traveling rates, and a lot more. By sticking to a well-defined WPS, welders can maintain harmony in their job, resulting in regular weld quality across different tasks.
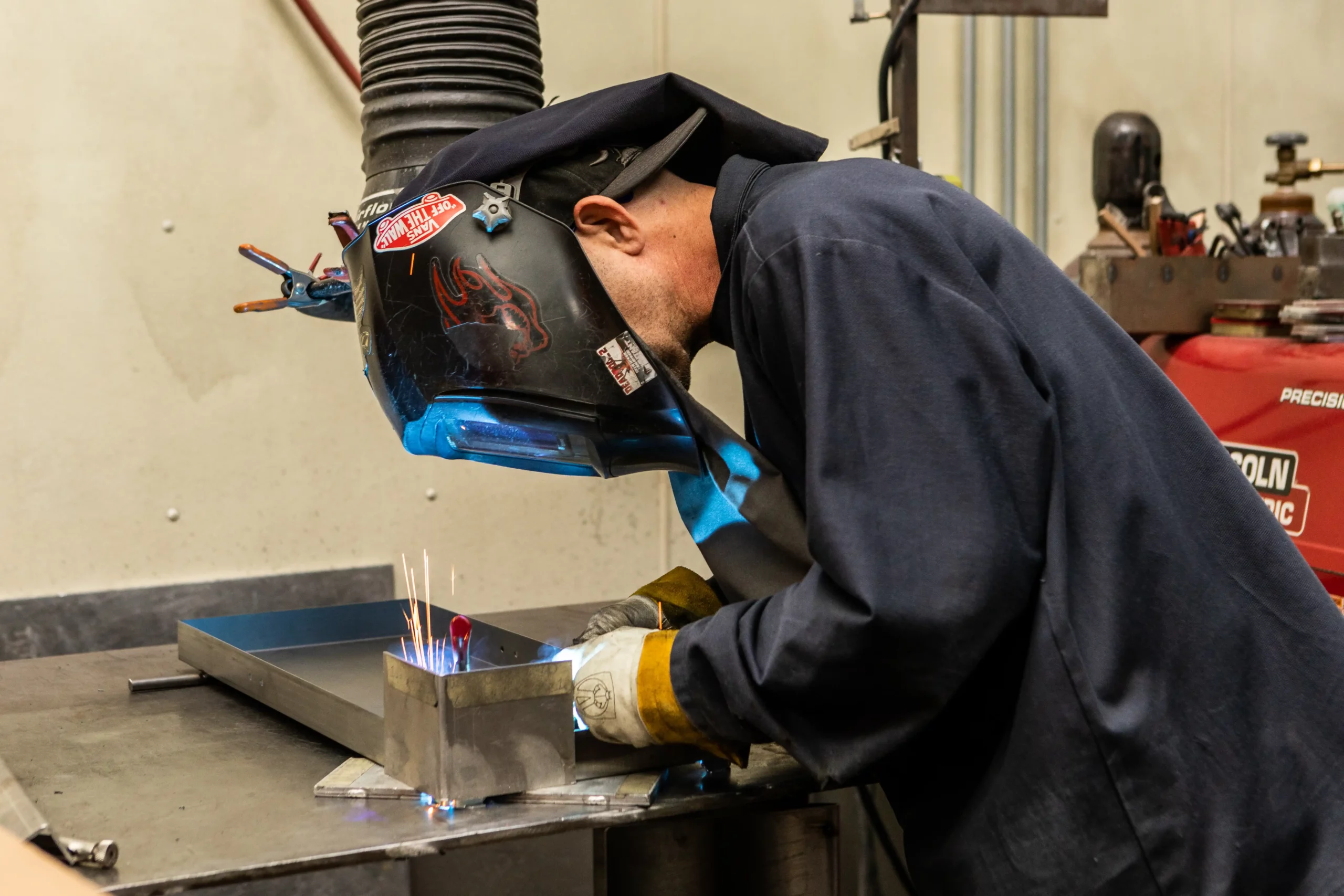
Crucial Element of WPS
Going over the essential parts of a welding treatment spec (WPS) is vital for recognizing its function in welding procedures. One crucial element of a WPS is the welding process spec, which details the specific welding procedures to be used, such as gas tungsten arc welding (GTAW) or protected metal arc welding (SMAW) By including these key aspects into the WPS, welding treatments can be standardized, guaranteeing high quality, performance, and safety in welding operations.
Approaches for WPS Optimization

Secondly, training and qualification of welding workers according to the certain requirements of the WPS is vital. Supplying extensive training programs and making sure that welders are certified to execute procedures laid out in the WPS can lead to higher high quality welds and lowered rework.
In addition, leveraging modern technology such as welding software program and monitoring systems can aid in maximizing WPS. These devices can help in tracking variables, ensuring specifications are within specified limitations, and supplying real-time comments to welders, allowing them to make immediate changes for boosted weld quality.
Usual Difficulties and Solutions
Encountering challenges in carrying out the strategies for WPS optimization can hinder welding operations' effectiveness and high quality. One typical obstacle is insufficient training or understanding of the welding procedure requirements (WPS) amongst the welding team.
One more challenge is the lack of appropriate documents and record-keeping, which is important for WPS optimization. Without clear records of welding specifications, materials utilized, and evaluation outcomes, it ends up being tough to recognize areas for improvement and make sure consistency in welding procedures. Applying a robust documents system, such as electronic welding monitoring software application, can assist improve record-keeping and help with data evaluation for continuous renovation.
Furthermore, irregular welding equipment calibration and you could look here maintenance can present a substantial obstacle to WPS optimization. Regular tools checks, calibration, and maintenance timetables should be complied with purely to guarantee that welding specifications are precisely regulated and kept within the specified tolerances (welding WPS). By resolving these typical challenges with proactive options, welding operations can enhance effectiveness, high quality, and total welding excellence
Finest Practices for WPS Application
To make sure effective WPS execution in welding operations, adherence to industry standards and careful attention to information are extremely important. When initiating WPS execution, it is vital to start by thoroughly recognizing the details welding needs of the task. This entails from this source an extensive testimonial of the welding treatment specifications, materials to be welded, and the environmental conditions in which the welding will occur.
Once the needs are clear, the following step is to select the appropriate welding treatment that aligns with these requirements. This entails getting in touch with the appropriate codes and standards, such as those given by the American Welding Culture (AWS) or the International Organization for Standardization (ISO), to ensure conformity and top quality.
Additionally, documenting the whole WPS application procedure is essential for traceability and quality control. Detailed documents need to be maintained concerning welding specifications, material preparation, interpass and preheat temperatures, welding consumables used, and any type of inconsistencies from the original treatment. Routine audits and evaluations of the WPS can aid determine areas for enhancement and make certain ongoing optimization of the welding process.


Verdict
Finally, the application and optimization of Welding Treatment Specifications (WPS) is important for achieving welding quality. By understanding the crucial elements of WPS, executing effective approaches for optimization, resolving common challenges, and complying with finest methods, welders can ensure premium welds and safe working problems. It is crucial for specialists in the welding market to prioritize the proper application of WPS to enhance total welding performance and accomplish wanted outcomes.
The Importance of Welding Procedure Specs (WPS) in the welding sector can not be overemphasized, serving as the foundation for making sure uniformity, top quality, and security in welding operations. A WPS supplies detailed guidelines on just how welding news is to be lugged out, consisting of essential variables such as materials, welding processes, joint design, filler steels, preheat and interpass temperatures, welding currents, voltages, travel speeds, and much more. One important element of a WPS is the welding process specification, which describes the certain welding processes to be made use of, such as gas tungsten arc welding (GTAW) or shielded steel arc welding (SMAW) By incorporating these key aspects into the WPS, welding procedures can be standardized, ensuring high quality, performance, and safety in welding procedures.
It is important for experts in the welding market to focus on the proper implementation of WPS to enhance general welding performance and attain desired end results.
Report this page